CSSD Productivity
- ESP Team
- Feb 11, 2019
- 3 min read
Updated: Mar 10, 2022
In my 28 yrs of managing sterile processing departments, I have been challenged with many different productivity models. In most cases, the models were designed to reduce staffing in the department. Comparisons were driven by internal and external hospital benchmarks. The problem with this is the old apples to oranges comparison, even when comparing sister hospitals. One of our sister hospital comparisons included a cardiac tray. One tray contained approximately 40 or so instruments, and the other hospital's like tray had well over 100 instruments. For data comparisons, each of the hospitals was given an equal amount of one tray processed for their productivity numbers. The equation then becomes items reprocessed (number of trays)/worked hours (not including non-productive hours). This is an unfair assessment. To explore some of these difficulties calculating productivity (productive work hours), let's explore the following issues.
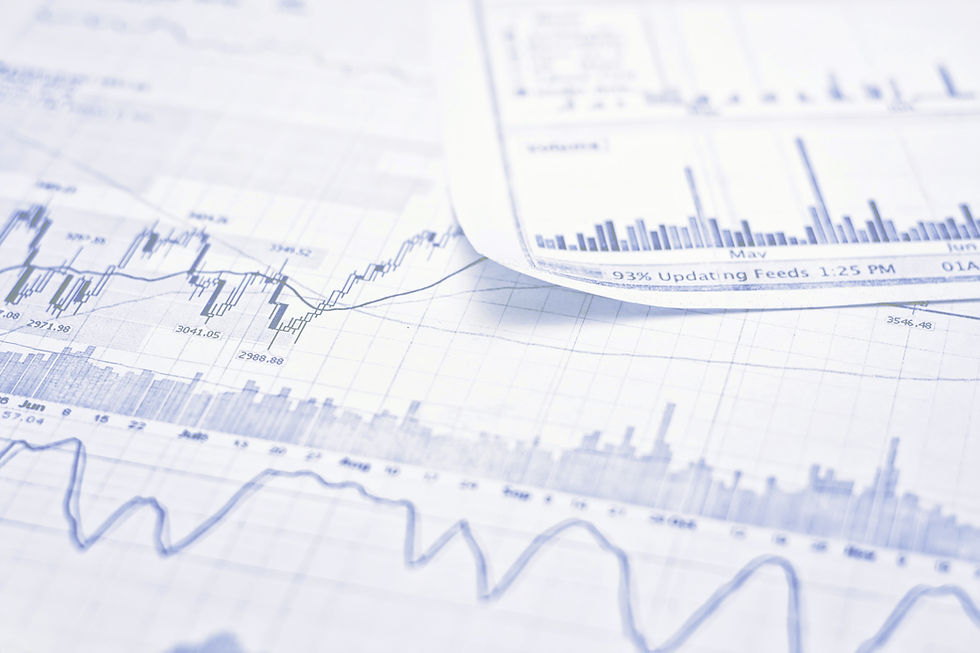
For hospitals without tracking systems, you must rely on manual counts. For starters, the staff must count the number of trays they are reproducing or better yet you can count the number of items sterilized. Inherently, you loose count on that actual number of instruments reproduced, being that peel pouches can vary in the count of instruments packaged, and obviously, trays do too. This process is also usually very time consuming, but with an excel spreadsheet, it can be accomplished. If your model includes a case cart metric (# of OR cases), you can still accomplish this process by averaging the number of items sterilized and dividing it by the total number of cases. You can use your averages to drive your metric. The most significant issue I see with this process is that not all items reprocessed come from the OR, as some come from other areas within the hospital. There are other options as in adding some time values to each tray or peel pouch produced (e.g., Lg. tray =20 mins, Med. Tray= 15 min, etc.). It will at least provide you with a productive hours work scenario (do forget to add time work in decontamination too).
Hospitals with tracking systems have a few more options than those listed above. First, it only takes a couple of minutes to run a report to determine what was reprocessed, with an added benefit of when. The "when" helps with mapping proper staffing models to help keep your push/pull model as neutral as possible. With several tracking systems, you can build into the database for each set a productivity number for both decontamination and prep/pack. Again, you can use a similar flat rate as described above, but for a more productive approach put in a mathematics equation for each instrument (e.g., 7 seconds for each instrument in decontamination and 14 seconds for each instrument in prep/pack). Now you are getting closer to the total number of productive hours needed to staff the department.The remaining time lost, as in not captured, is crucial to your final productive worked hours. Here is a list of often forgotten items:
Case Carts
Equipment cleaned
Deliveries
Sterilization Loads
Hand wash (may need additional time in decontamination)
Implant trays (extra time for restocking)
Laparoscopic trays (extra time for insulation testing)
This is not an exhaustive list.
Lastly, an agreed-upon percentage for productivity for each hospital needs to be established. No one works at a 100% productivity rate. As soon as someone is interrupted their productivity drops below 100%. Another example would be, if the instruments come back from the operating room not in the trays that they were sent in hours are lost searching for the correct instruments. Each hospital will vary in their lost worked hours by design of the department, how instruments are returned to CSSD, tracking methods, inspection tools, etc. In previous hospitals that I have worked in the agreed productivity percentages were around 80%-85% in decontamination and about 70%-75% in prep/pack. Benchmarks comparisons are useful to see where you stand as an overall big picture scenario, but it is generally and apples to oranges comparison.
At Evolved Sterile Processing, our consultants have a greater focus on sterile processing. With our decades of experience, we will help you develop better processes and educational resources for your staff.
Comments